在半導(dǎo)體制造業(yè)中,晶圓作為芯片的基礎(chǔ)材料,其表面質(zhì)量直接決定了最終產(chǎn)品的性能和可靠性。隨著技術(shù)的不斷進(jìn)步,
晶圓表面缺陷檢測(cè)系統(tǒng)已成為確保產(chǎn)品質(zhì)量的關(guān)鍵環(huán)節(jié)。其中,切割槽的深度與寬度檢測(cè)是評(píng)估晶圓加工精度和完整性的一項(xiàng)重要指標(biāo)。
切割槽是在晶圓制造過程中,為了分離不同的芯片或進(jìn)行后續(xù)工藝而刻蝕的微小溝槽。這些溝槽的尺寸精度對(duì)于芯片的封裝、互聯(lián)以及整體性能具有重要影響。傳統(tǒng)的檢測(cè)方法往往依賴于人工目視或使用簡(jiǎn)單的機(jī)械測(cè)量工具,這些方法不僅效率低下,而且容易受到人為因素的影響,導(dǎo)致測(cè)量結(jié)果的不準(zhǔn)確。
為了克服這些挑戰(zhàn),晶圓表面缺陷檢測(cè)系統(tǒng)引入了先進(jìn)的圖像處理和機(jī)器學(xué)習(xí)技術(shù)。通過高分辨率的光學(xué)顯微鏡或電子顯微鏡,系統(tǒng)能夠捕捉到晶圓表面的微小細(xì)節(jié),包括切割槽的形貌特征。隨后,利用圖像處理算法對(duì)捕捉到的圖像進(jìn)行預(yù)處理,如去噪、增強(qiáng)對(duì)比度等,以提高后續(xù)分析的準(zhǔn)確性。
在圖像預(yù)處理的基礎(chǔ)上,系統(tǒng)采用特征提取技術(shù)來識(shí)別切割槽的邊緣,并計(jì)算其深度和寬度。這一步驟通常依賴于邊緣檢測(cè)算法,如Canny算子、Sobel算子等,它們能夠精確地定位切割槽的邊緣位置。通過對(duì)邊緣位置的進(jìn)一步分析,系統(tǒng)可以計(jì)算出切割槽的深度和寬度值,并將這些值與預(yù)設(shè)的規(guī)格進(jìn)行比較,以判斷其是否符合要求。
此外,系統(tǒng)還結(jié)合了機(jī)器學(xué)習(xí)算法,通過對(duì)大量歷史數(shù)據(jù)的訓(xùn)練和學(xué)習(xí),系統(tǒng)能夠自動(dòng)識(shí)別和分類不同類型的切割槽缺陷,如過深、過寬、不規(guī)則形狀等。這種智能化的檢測(cè)方式不僅提高了檢測(cè)的準(zhǔn)確性和效率,還大大降低了人為因素對(duì)檢測(cè)結(jié)果的影響。
最后為您展示一組晶圓表面缺陷檢測(cè)系統(tǒng)圖片,以便您更好地了解它!
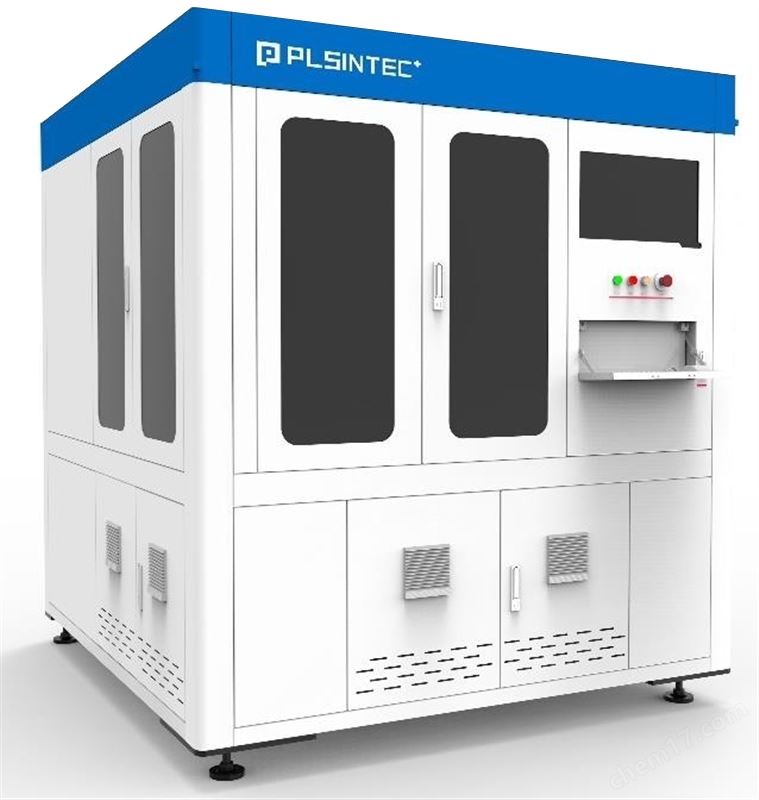
綜上所述,晶圓表面缺陷檢測(cè)系統(tǒng)中的切割槽深度與寬度檢測(cè)技術(shù)對(duì)于確保半導(dǎo)體產(chǎn)品的質(zhì)量和可靠性具有重要意義。隨著技術(shù)的不斷發(fā)展,這些檢測(cè)技術(shù)將更加智能化、自動(dòng)化,為半導(dǎo)體制造業(yè)的持續(xù)發(fā)展提供有力支持。同時(shí),我們也期待未來能夠出現(xiàn)更多創(chuàng)新性的檢測(cè)技術(shù),以應(yīng)對(duì)日益復(fù)雜的晶圓加工需求和不斷提高的產(chǎn)品質(zhì)量標(biāo)準(zhǔn)。